From Principles to Applications- Led Gold Wire Bonding Technical Analysis
Introduction: How Do Tiny Gold Wires Support the “Lifeline” of LEDs?
LEDs (Light Emitting Diodes) are at the heart of modern lighting and display technologies, with their performance and lifespan heavily relying on packaging processes. Between the chip and external circuitry lies a gold wire with a diameter less than 1/10th of a human hair, responsible for transmitting current and ensuring stable operation. Gold Wire Bonding technology acts as the “invisible guardian” ensuring high reliability in LEDs.
However, with the explosion of Mini LED/Micro LED technologies, bonding precision requirements have evolved from micrometric to submicrometric levels. The cost of gold wire material accounts for 15%-20% of the total packaging cost, presenting a dual challenge of “performance” and “cost” for the industry. This article delves into this critical technology, revealing the scientific logic and industrial dynamics behind it.
1. Technical Principles and Advantages of Gold Wire Bonding
1. Material Selection: Why Gold Instead of Copper or Aluminum?
Gold wire is unmatched as a bonding material due to three main properties:
- Conductivity: Gold has a resistivity of only 2.44 μΩ·cm (compared to 1.68 μΩ·cm for copper but with poorer oxidation resistance), reducing current transmission losses.
- Ductility: Gold wire can be stretched to a diameter of 15μm without breaking, accommodating ultra-dense soldering requirements (e.g., Mini LED spacing <0.5mm).
- Stability: It does not oxidize in extreme temperatures ranging from -40°C to 150°C, avoiding the risk of circuit breaks due to corrosion.
Comparative experiments show that LED modules bonded with copper wire exhibited a failure rate more than three times greater than those with gold wire after aging for 1000 hours at 85°C/85% humidity (source: Study on Semiconductor Device Reliability).
2. Process Realization: The Precise “Dance” of Thermocompression and Ultrasonication
- Thermocompression Bonding: By applying heat (200-300°C) and pressure, the gold wire and pad metal atoms diffuse and bond. The advantage lies in its high connection strength, making it suitable for power-type LEDs.
- Ultrasonic Bonding: High-frequency vibrations (60-120kHz) create heat through friction, eliminating the need for external heating and preventing thermal damage to the chip, making it ideal for sensitive devices like Micro LEDs.
Core process parameters control (example):
Parameter | Typical Values for Thermocompression | Typical Values for Ultrasonic Bonding |
---|---|---|
Temperature | 250°C | Room Temperature |
Pressure | 0.5-1.5N | 0.3-0.8N |
Time | 10-50ms | 20-100ms |
2. Quality Verification: The “Eagle Eye” from the Laboratory to the Production Line
1. Physical Testing Methods
- Microscopic Observation: Inspection of bond morphology (see Figure 1), with requirements for no cracks and uniformly constricted necks.
- Tensile Testing: According to JEDEC standards, a 25μm gold wire should withstand a tensile force of ≥3gf (some brands’ wire bonders have an average measured value of 4.2gf).
2. Chemical Analysis Methods
Referencing “LED Display Acceptance Testing Technology,” a laboratory verified suspected copper-doped LED samples as follows:
- Acid Dissolution: Aqua regia was used to dissolve the bonding points and extract metal components.
- ICP-AES Detection: The gold content was measured at 98.7%, with copper at 1.3%.
- Theoretical Value Calculation: Based on gold wire density (19.3g/cm3) and diameter (25μm), the calculated single bonding point gold wire length should be 1.02mm, with a discrepancy of only 2.9% from the reference value of 1.05mm, confirming the use of pure gold technology.
Industry Warning: Some companies reduce costs by substituting gold wire with gold-plated copper wire, showing similar initial performance. However, after one year, oxidation rates at the bonding point can reach 30% (according to sampling data from a quality inspection agency in 2024).
3. Cost Dilemmas and Technical Innovations
1. Feasibility Disputes of Alternative Materials
- Copper Wires: Cost only 1/8 that of gold, but require additional coatings for protection (e.g., palladium, nickel), increasing process complexity.
- Silver Alloys: Offer better conductivity than gold but are prone to sulfide-induced discoloration, currently used only in low-end lighting applications.
2. Pathways for Process Upgrades
- Equipment Precision Improvement: Domestic wire bonders’ positioning accuracy improved from ±5μm (2020) to ±1μm (2024), achieving bonding yields exceeding 99.9%.
- Composite Bonding Technology: Laser-assisted welding can reduce bonding time by 40%, applied to automotive-grade LED modules (e.g., Tesla Model 3 tail lights).
4. Application Scenarios and Future Trends
1. Indispensable in High-End Fields
- Automotive Lighting: The Mercedes-Benz EQS headlights utilize dual gold wire bonding to ensure cold starts at -40°C without failure.
- AR/VR Micro Displays: Bonding points with diameters <5μm can only be satisfied using gold wire precision requirements.
2. Technology Outlook
- Nanoscale Bonding: Utilizing nano gold wire (diameter <100nm) to achieve ultra-high-density interconnections, supporting 10,000 PPI micro displays.
- Intelligent Detection: AI visual systems for real-time analysis of bonding morphology could replace 90% of manual quality inspections (based on ASM’s 2025 roadmap).
Conclusion: The “Offensive and Defensive Strategy” of Gold Wire Bonding
Despite cost pressures, gold wire bonding continues to maintain a dominant position in high-end LED fields due to its physical properties and mature processes. In the future, through material innovations (such as gold-silver composite wires) and equipment intelligence, this classic technology may be revitalized, continuing to illuminate the future of the semiconductor industry.
Led Gold Wire Bonding Machine
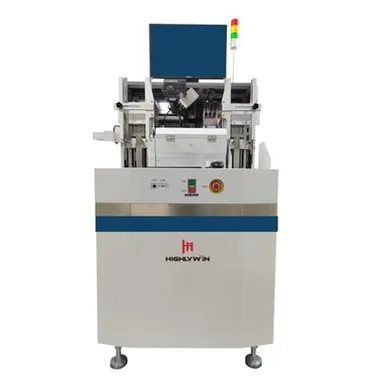
HIGHLYWIN is a leading provider of design, custom engineering, and manufacturing solutions, specializing in SMT machine. We pride ourselves on offering comprehensive support services and spare parts in the SMT field, making us your trusted one-stop solution supplier.
References
- “LED Display Acceptance Testing Technology,” China Quality Inspection Publishing House, 2023.
- JEDEC JESD22-B116, Wire Bond Shear Test Method.
- TrendForce report “2025 Global LED Packaging Materials Market Outlook.”