Introducción: Una revolución manufacturera en el microcosmos
Desde procesadores de teléfonos inteligentes y placas de control de dispositivos médicos hasta sensores electrónicos automotrices, la creación de este hardware de precisión se basa en Tecnología de montaje superficial (SMT)En comparación con la tecnología tradicional de orificio pasante (THT), la tecnología SMT ha impulsado la industria electrónica con tres innovaciones clave:
- Miniaturización:Los tamaños de los componentes se han reducido a 01005 (0,4 × 0,2 mm), lo que permite densidades de ensamblaje varias veces superiores a THT.
- Automatización de alto nivelLas máquinas de selección y colocación de primer nivel pueden alcanzar velocidades de 250.000 CPH (componentes por hora) con una precisión de colocación que alcanza el nivel de ±15 μm.
- Alta confiabilidad:Las uniones de soldadura formadas mediante soldadura por reflujo ofrecen una resistencia mecánica y un rendimiento eléctrico superiores, con una consistencia que supera ampliamente la soldadura manual.
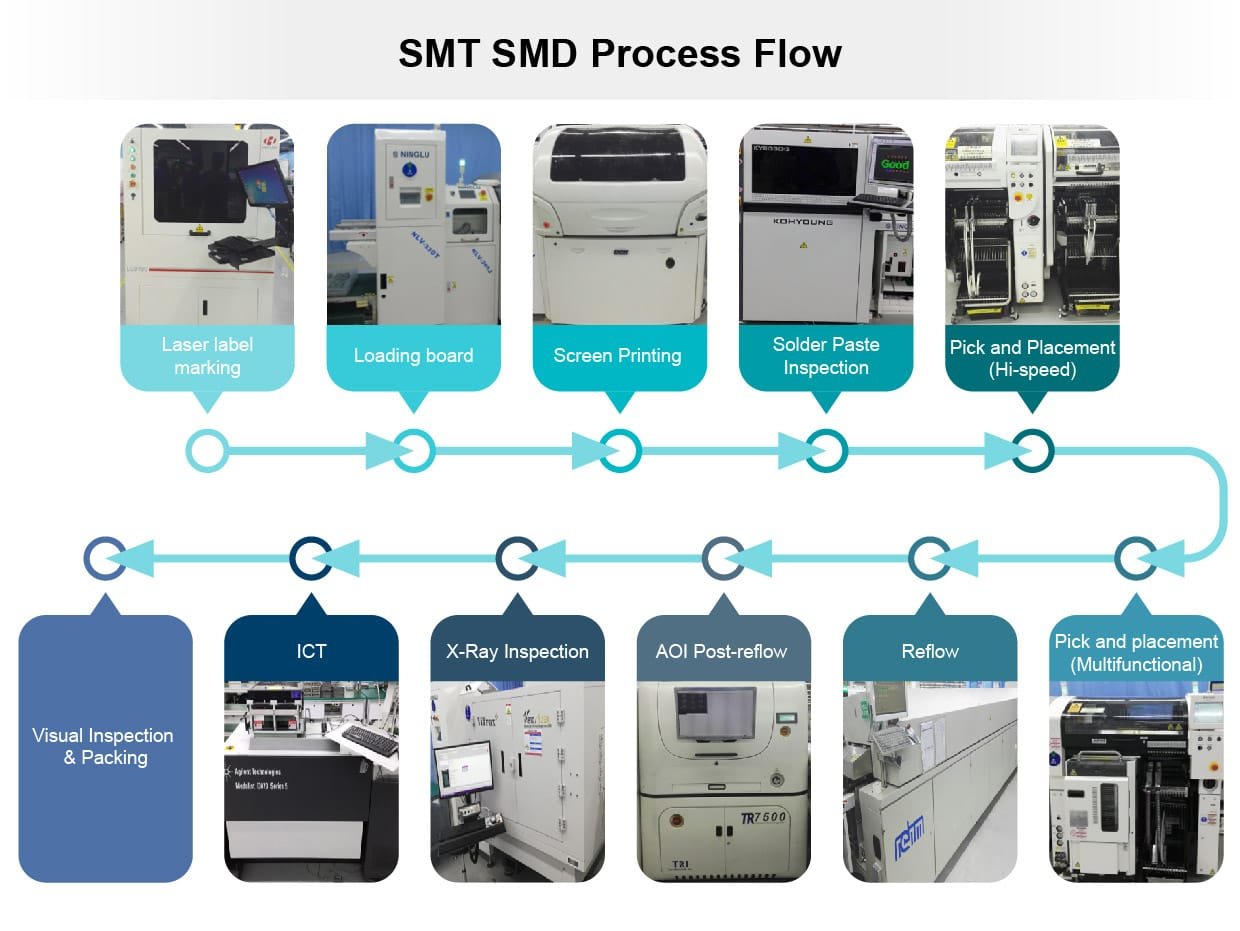
I. Descripción general del diagrama de flujo del proceso SMT
Un proceso SMT completo funciona como una línea de montaje de precisión donde cada etapa es crítica.
gráfico LR A[Carga de PCB (cargador)] --> B[Impresión de pasta de soldadura (impresora)] B --> C[3D SPI (inspección de pasta de soldadura)] C --> D[Colocación de componentes (montador)] D --> E[Soldadura por reflujo (horno de reflujo)] E --> F[AOI (inspección óptica automatizada)] F --> G{¿Tiene BGA/QFN u otras juntas ocultas?} G -- Sí --> H[Inspección por rayos X] H --> I[Descarga/siguiente proceso] G -- No --> I
II. Explicación de los pasos principales del proceso SMT
Paso 1: Carga y preprocesamiento de PCB
- Equipo claveCargador automático de PCB
- Fundamentos del preprocesamiento:
- Hornear para deshumidificar:Normalmente se hornea a 125 °C durante varias horas para eliminar la humedad del sustrato y los componentes de la PCB, lo que evita que se produzcan “palomitas” (delaminación) durante la soldadura a alta temperatura.
- Protección ESD:El entorno debe tener controles estrictos de temperatura y humedad (por ejemplo, humedad 45%-70%), y todo el personal debe usar muñequeras ESD para proteger los componentes sensibles.
Paso 2: Impresión de pasta de soldadura: donde la precisión determina el éxito
Este paso aplica con precisión una cantidad definida de pasta de soldadura sobre las almohadillas de la PCB, preparándolas para la soldadura de los componentes.
Elemento | Ejemplo de especificaciones técnicas | Impacto |
---|---|---|
Plantilla | Corte por láser, precisión de apertura ±5 μm, pulido electrolítico. | Garantiza una alta eficiencia de transferencia de pasta de soldadura (>90%) y una definición de impresión limpia. |
Pasta de soldadura | Polvo tipo 4, tamaño (20-38 μm), viscosidad 800-1000 kcps | Reduce los riesgos de hundimientos y formación de puentes después de la impresión. |
Enjugador de goma | Poliuretano o metal, dureza 80-90 Shore A, ángulo 45°-60° | Garantiza un espesor de impresión uniforme y consistente. |
Paso 3: SPI: la primera línea de defensa contra defectos de soldadura
SPI (inspección de pasta de soldadura) utiliza tecnología óptica 3D para inspeccionar el volumen, el área, la altura y la forma de la pasta de soldadura en cada almohadilla, lo que lo convierte en un punto crítico de control del proceso.
Ejemplo de lógica # para una comprobación de aprobación/rechazo de una inspección de pasta de soldadura. def check_paste(paste_data): # Nota: Los umbrales se definen según los requisitos específicos del producto y del proceso. height_ok = 0.08 <= paste_data.height <= 0.15 # en mm. volume_ok = paste_data.volume_percent >= 70. area_ok = paste_data.area_coverage >= 80. if height_ok and volume_ok and area_ok: return "PASS" else: # Activa una alarma y solicita la limpieza de la plantilla o el ajuste de parámetros. return "FAIL - Trigger Alarm"

Las estadísticas de la industria muestran que SPI puede prevenir más de 70% de posibles defectos de soldadura causados por una impresión deficiente de la pasta de soldadura.
Paso 4: Colocación de componentes: un juego de precisión micrométrica
- Equipo clave:Máquina de selección y colocación (o montadora), disponible como disparadores de chips de alta velocidad y montadores flexibles de alta precisión.
- Tecnologías centrales:
- Alineación de la visión:Utiliza cámaras para reconocer marcas fiduciales en la PCB y los cables de los componentes para una colocación de alta precisión (la precisión común es ±0,05 mm).
- Tecnología de boquillas:Cambia automáticamente las boquillas en función del tamaño y la forma del componente y las recoge con un sistema de vacío.
- A prueba de errores:Verifica la información de los componentes al escanear códigos de barras en los alimentadores para evitar piezas incorrectas; utiliza cámaras o sensores láser sobre la marcha para verificar la orientación de los componentes, evitando el tombstoning o la inversión de polaridad.
Paso 5: Soldadura por reflujo: el arte del perfil térmico
La placa de circuito impreso (PCB), con sus componentes, pasa por un horno tipo túnel con múltiples zonas de calentamiento. La pasta de soldadura se funde y luego se enfría para formar conexiones eléctricas y mecánicas fiables.
Un perfil térmico ideal (ejemplo para soldadura sin plomo SAC305):
gráfico TD A (Entrada) --> B [Rampa de precalentamiento de la zona a 150-180 °C 60-90 s] B --> C [Mantener la zona de remojo/activación a 180-220 °C 60-120 s] C --> D [Temperatura máxima de la zona de reflujo 240-250 °C 45-60 s por encima del líquido] D --> E [Velocidad de enfriamiento de la zona de enfriamiento < 4 °C/s] E --> F (Salida)

Para tableros de alta densidad o sensibles al calor, Nitrógeno (N₂) Se utiliza a menudo para crear una atmósfera inerte. Mantener los niveles de oxígeno extremadamente bajos (p. ej., <500 ppm) reduce la oxidación y mejora la calidad de la unión soldada.
Paso 6: AOI – El inspector de visión inteligente
La AOI (inspección óptica automatizada) se realiza después del reflujo para inspeccionar automáticamente la PCBA en busca de defectos de soldadura.
- Defectos detectados:Componentes faltantes, piezas incorrectas, polaridad invertida, desplazamiento de componentes, daño por desecho, puenteo, bolas de soldadura y soldadura insuficiente.
- Evolución tecnológicaLos sistemas AOI modernos utilizan cada vez más algoritmos de IA basados en aprendizaje profundo. Entrenados con extensas bibliotecas de imágenes de defectos, mejoran significativamente la precisión de detección y reducen las llamadas falsas.
Paso 7: Inspección por rayos X (para uniones de soldadura ocultas)
Para componentes como BGA, QFN y LGA con uniones soldadas bajo el encapsulado, la AOI no es efectiva. La inspección por rayos X puede penetrar el chip para visualizar claramente las conexiones internas de las bolas de soldadura.
- Puntos clave de inspección:Cortocircuitos de soldadura, circuitos abiertos (no húmedos) y el tamaño y porcentaje de huecos (por ejemplo, los estándares IPC pueden requerir que los huecos sean <25%).
III. SMT de una cara vs. de dos caras: Comparación de procesos
Dependiendo del diseño del producto, los PCBA pueden ser de una o dos caras, siendo estas últimas un proceso más complejo.
Diferencia de proceso | Montaje de un solo lado | Montaje de doble cara (primero la parte superior, luego la inferior) |
---|---|---|
Proceso del primer lado (superior) | Flujo SMT completo (Imprimir → Colocar → Reflujo) | Flujo SMT completo (Imprimir → Colocar → Reflujo) |
Tablero volteando | N / A | Utiliza un módulo inversor dedicado en la línea para una transición suave. |
Proceso del segundo lado (inferior) | N / A | Otro ciclo completo de Imprimir → Colocar → Reflujo. |
Desafío clave | - | Controlar el segundo perfil de reflujo para evitar que los componentes del lado superior (ahora colgados boca abajo) se caigan, especialmente los más pesados. |
Aplicación típica | Placas más simples como controles remotos, fuentes de alimentación. | Productos de alta densidad como placas base de teléfonos inteligentes, computadoras portátiles y módulos de comunicación. |
IV. Análisis de defectos de SMT y fortalecimiento de la calidad
Las 4 principales soluciones para defectos
Tipo de defecto | Causa raíz típica | Acción correctiva/preventiva |
---|---|---|
Tumbas | Masa térmica desigual en las dos almohadillas de un componente, lo que provoca que la soldadura se derrita en diferentes momentos. | Optimizar el diseño de la almohadilla de PCB para la simetría térmica (DFM); optimizar la zona de precalentamiento por reflujo. |
Bolas de soldadura | Humedad en la pasta de soldadura o fundente demasiado agresivo; la velocidad de rampa de precalentamiento es demasiado rápida. | Almacene y manipule la pasta de soldadura de acuerdo con las especificaciones; reduzca la velocidad de la rampa de precalentamiento. |
Unión de soldadura en frío | Temperatura máxima o tiempo insuficiente en la zona de reflujo; oxidación de la almohadilla. | Optimizar el perfil térmico de reflujo; garantizar una buena soldabilidad de PCB y componentes. |
Anulación de BGA | Los volátiles del fundente no logran escapar completamente antes de que la unión de soldadura se solidifique. | Utilice pasta de soldadura con baja formación de huecos; optimice el diseño de la apertura de la plantilla (por ejemplo, paneles de ventanas); optimice el perfil térmico. |
Los pilares gemelos de los sistemas de calidad
- DFM (Diseño para Fabricabilidad)
- Considerar las limitaciones del proceso de fabricación durante la fase de diseño del producto, como el espaciado de los componentes, el diseño de las almohadillas y la ubicación fiducial.
- Implementación del estándar IPC
- Adherirse a los estándares de ensamblaje de productos electrónicos reconocidos internacionalmente, como IPC-A-610 (Aceptabilidad de Ensamblajes Electrónicos) y J-STD-001 (Requisitos para conjuntos eléctricos y electrónicos soldados).
V. Tendencias emergentes en SMT
- Fábrica inteligente e industria 4.0:Conectar todos los equipos a través de un MES (sistema de ejecución de fabricación) para el monitoreo de datos en tiempo real, trazabilidad y toma de decisiones inteligente para optimizar la OEE (eficacia general del equipo).
- Integración de paso fino y heterogénea:Creciente demanda de ensamblaje de componentes sub-01005 y módulos SiP (sistema en paquete) de alta densidad.
- Fabricación ecológica:Uso de fundentes con bajo contenido de COV o que no requieren limpieza y equipos energéticamente eficientes para reducir el impacto ambiental.
Conclusión: El camino del refinamiento nunca termina
Cuando una placa base de alta densidad con miles de componentes fluye eficientemente por una línea SMT, representa una fusión perfecta de ciencia de materiales, ingeniería de precisión, óptica y software. Dominar el proceso SMT es fundamental para acceder al mundo de la fabricación electrónica moderna. Solo adoptando continuamente la innovación tecnológica se puede prosperar en este camino de mejora continua.
Apéndice: Preguntas frecuentes (FAQ)
P1: ¿Cómo elegir una máquina pick-and-place?
R: Las métricas clave incluyen la velocidad teórica (CPH), el rendimiento real (UPH), la precisión de colocación (μm), la gama de componentes compatibles y el tiempo de cambio. La elección depende de una evaluación exhaustiva del tipo de producto y el volumen de producción.
P2: ¿El proceso adhesivo (pegamento rojo) está obsoleto?
R: En el ensamblaje de tecnología mixta (SMT + THT) que requiere soldadura por ola, el proceso adhesivo sigue siendo indispensable para asegurar los componentes SMT. Sin embargo, rara vez se utiliza en procesos de refusión de doble cara.
P3: ¿Es necesaria la inspección SPI del 100%?
R: Para productos de alta confiabilidad (p. ej., automotrices, médicos, aeroespaciales) y PCBA de alta densidad y paso fino, es obligatorio el SPI 100%. La industria automotriz suele requerir un índice de capacidad de proceso (Cpk) ≥ 1,67, lo que implica una tasa de defectos potencial extremadamente baja que solo puede garantizarse mediante la inspección 100%.
P4: ¿Cómo se puede optimizar el consumo energético del horno de reflujo?
R: Los hornos de reflujo modernos pueden ser 30% más eficientes energéticamente que los modelos más antiguos gracias al uso de sistemas de recuperación de calor de múltiples etapas, materiales de aislamiento mejorados y modos de espera inteligentes.
Tome acción ahora:
Obtenga su lista de verificación DFM de línea SMT
¡Suscríbete a nuestro Electronics Manufacturing Weekly para descubrir más secretos del proceso!
(Nota: Los datos de este artículo se citan de estándares IPC, documentos técnicos sobre equipos y mejores prácticas de la industria. Algunas cifras son ejemplos típicos; los valores reales dependen del proceso específico).