Introduction : Une révolution industrielle dans le microcosme
Des processeurs de smartphones et des cartes de contrôle d'appareils médicaux aux capteurs électroniques automobiles, la création de ce matériel de précision repose sur Technologie de montage en surface (CMS). Par rapport à la technologie traditionnelle à trous traversants (THT), la technologie SMT a fait progresser l'industrie électronique avec trois innovations clés :
- Miniaturisation:Les tailles des composants ont été réduites à 01005 (0,4 × 0,2 mm), permettant des densités d'assemblage plusieurs fois supérieures à celles du THT.
- Automatisation de haut niveau:Les machines de prélèvement et de placement haut de gamme peuvent atteindre des vitesses de 250 000 CPH (composants par heure) avec une précision de placement atteignant le niveau de ± 15 μm.
- Haute fiabilité:Les joints de soudure formés par soudure par refusion offrent une résistance mécanique et des performances électriques supérieures, avec une cohérence dépassant de loin la soudure manuelle.
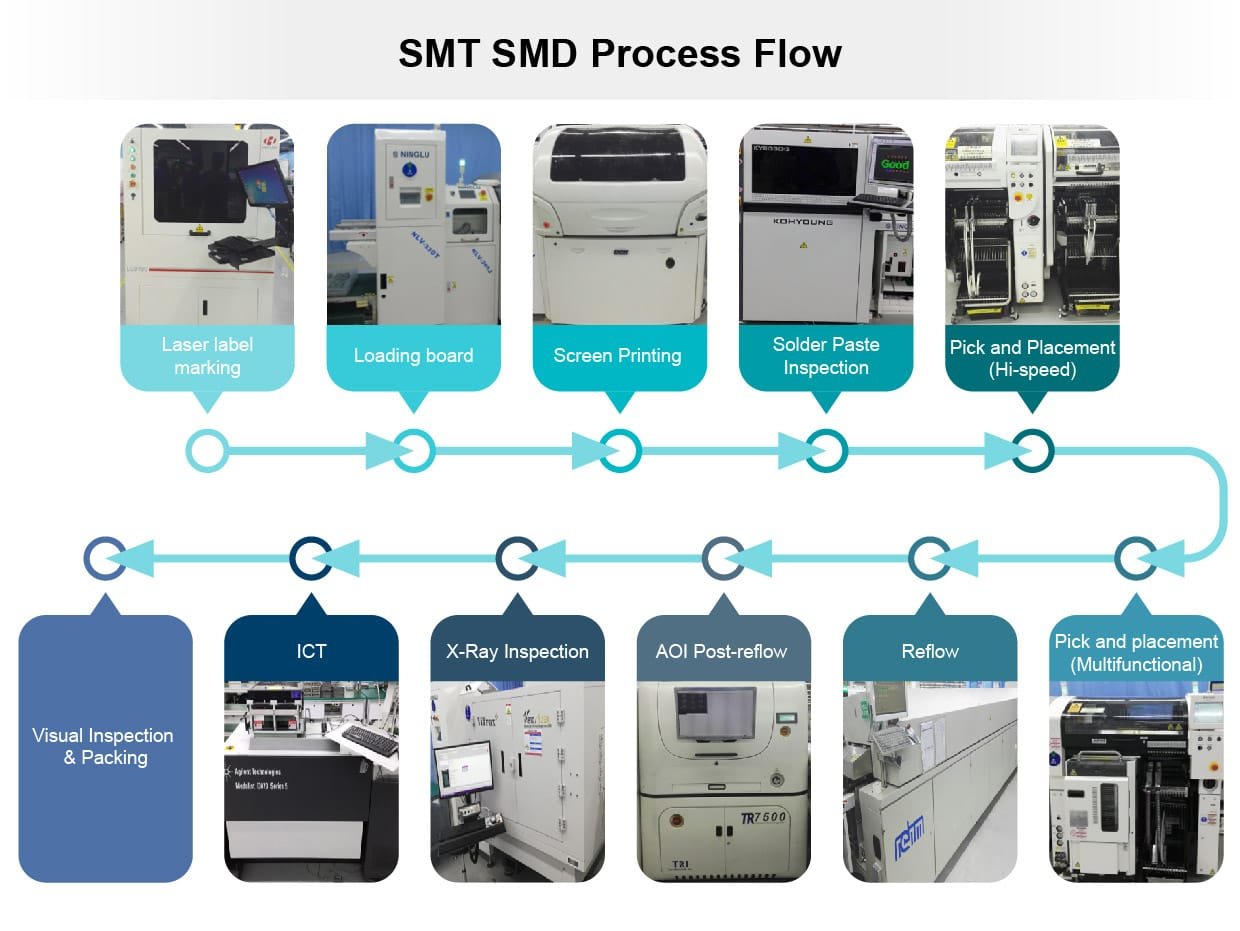
I. Présentation du diagramme de processus SMT
Un processus SMT complet fonctionne comme une chaîne de montage de précision où chaque étape est critique.
graphique LR A[Chargement PCB (chargeur)] --> B[Impression de pâte à souder (imprimante)] B --> C[SPI 3D (inspection de pâte à souder)] C --> D[Placement des composants (monteur)] D --> E[Soudage par refusion (four à refusion)] E --> F[AOI (inspection optique automatisée)] F --> G{A des joints BGA/QFN ou autres joints cachés ?} G -- Oui --> H[Inspection aux rayons X] H --> I[Déchargement / Processus suivant] G -- Non --> I
II. Étapes principales du processus SMT expliquées
Étape 1 : Chargement et prétraitement du PCB
- Équipement clé: Chargeur automatique de circuits imprimés
- Essentiels du prétraitement:
- Cuisson pour déshumidification:Cuisson généralement à 125 °C pendant plusieurs heures pour éliminer l'humidité du substrat et des composants du PCB, évitant ainsi le « popcorning » (délaminage) lors du soudage à haute température.
- Protection ESD:L'environnement doit avoir des contrôles stricts de température et d'humidité (par exemple, humidité 45%-70%), et tout le personnel doit porter des bracelets antistatiques pour protéger les composants sensibles.
Étape 2 : Impression de pâte à souder – Quand la précision est essentielle au succès
Cette étape applique précisément une quantité définie de pâte à souder sur les pastilles du PCB, les préparant ainsi à la soudure des composants.
Élément | Exemples de spécifications techniques | Impact |
---|---|---|
Pochoir | Découpe laser, précision d'ouverture ±5 μm, électropoli | Assure une efficacité de transfert de pâte à souder élevée (> 90%) et une définition d'impression nette. |
pâte à souder | Poudre de type 4 (20-38 μm), viscosité 800-1000 kcps | Réduit les risques d’affaissement et de pontage après l’impression. |
Raclette | Polyuréthane ou métal, dureté 80-90 Shore A, angle 45°-60° | Garantit une épaisseur d'impression uniforme et constante. |
Étape 3 : SPI – La première ligne de défense contre les défauts de soudure
SPI (Solder Paste Inspection) utilise la technologie optique 3D pour inspecter le volume, la surface, la hauteur et la forme de la pâte à souder sur chaque pastille, ce qui en fait un point de contrôle de processus critique.
# Exemple de logique pour une vérification de réussite/échec d'inspection de pâte à braser def check_paste(paste_data): # Remarque : les seuils sont définis par les exigences spécifiques du produit et du processus. height_ok = 0,08 <= paste_data.height <= 0,15 # en mm volume_ok = paste_data.volume_percent >= 70 area_ok = paste_data.area_coverage >= 80 si height_ok et volume_ok et area_ok : renvoie « RÉUSSITE » sinon : # Déclencher une alarme et demander le nettoyage du pochoir ou le réglage des paramètres renvoyer « ÉCHEC - Déclencher l'alarme »

Les statistiques de l'industrie montrent que le SPI peut empêcher plus de 70% de défauts de soudure potentiels causés par une mauvaise impression de pâte à souder.
Étape 4 : Placement des composants – Un jeu de précision au micron près
- Équipement clé:Machine Pick-and-Place (ou Mounter), disponible sous forme de tireurs de puces à grande vitesse et de monteurs flexibles de haute précision.
- Technologies de base:
- Alignement de la vision:Utilise des caméras pour reconnaître les repères sur le PCB et les fils des composants pour un placement de haute précision (la précision courante est de ± 0,05 mm).
- Technologie des buses:Change automatiquement les buses en fonction de la taille et de la forme des composants, en les récupérant avec un système de vide.
- Anti-erreurs: Vérifie les informations des composants en scannant les codes-barres sur les alimentateurs pour éviter les mauvaises pièces ; utilise des caméras à la volée ou des capteurs laser pour vérifier l'orientation des composants, évitant ainsi le tombstoneing ou l'inversion de polarité.
Étape 5 : Soudure par refusion – L'art du profil thermique
Le circuit imprimé, sur lequel sont placés les composants, traverse un four tunnel doté de plusieurs zones de chauffage. La pâte à braser fond puis refroidit pour former des connexions électriques et mécaniques fiables.
Un profil thermique idéal (exemple pour la soudure SAC305 sans plomb) :
graphique TD A(Entrée) --> B[Rampe de la zone de préchauffage à 150-180°C 60-90s] B --> C[Maintien de la zone de trempage/activation à 180-220°C 60-120s] C --> D[Température de pointe de la zone de refusion 240-250°C 45-60s au-dessus du liquidus] D --> E[Vitesse de refroidissement de la zone de refroidissement < 4°C/s] E --> F(Sortie)

Pour les cartes à haute densité ou sensibles à la chaleur, Azote (N₂) est souvent utilisé pour créer une atmosphère inerte. Maintenir des niveaux d'oxygène extrêmement bas (par exemple, < 500 ppm) réduit l'oxydation et améliore la qualité des soudures.
Étape 6 : AOI – L'inspecteur de vision intelligent
L'AOI (Automated Optical Inspection) est effectuée après la refusion pour inspecter automatiquement le PCBA à la recherche de défauts de soudure.
- Défauts détectés:Composants manquants, pièces incorrectes, polarité inversée, décalage de composant, tombstoneing, pontage, billes de soudure et soudure insuffisante.
- Évolution technologiqueLes systèmes AOI modernes utilisent de plus en plus d'algorithmes d'IA basés sur l'apprentissage profond. Entraînés sur de vastes bibliothèques d'images de défauts, ils améliorent considérablement la précision de la détection et réduisent les faux appels.
Étape 7 : Inspection aux rayons X (pour les soudures cachées)
Pour les composants tels que les BGA, les QFN et les LGA avec des soudures sous le boîtier, l'AOI est inefficace. L'inspection par rayons X permet de pénétrer la puce et de visualiser clairement les connexions internes des billes de soudure.
- Points d'inspection clés: Courts-circuits de soudure, circuits ouverts (non mouillés) et taille et pourcentage de vides (par exemple, les normes IPC peuvent exiger que les vides soient < 25%).
III. CMS simple face vs double face : comparaison des processus
Selon la conception du produit, les PCBA peuvent être simple face ou double face, ce dernier impliquant un processus plus complexe.
Différence de processus | Assemblage unilatéral | Assemblage double face (haut d'abord, puis bas) |
---|---|---|
Processus du premier côté (en haut) | Flux SMT complet (Impression → Placement → Refusion) | Flux SMT complet (Impression → Placement → Refusion) |
retournement de plateau | N / A | Utilise un module onduleur dédié dans la ligne pour une transition en douceur. |
Processus du deuxième côté (en bas) | N / A | Un autre cycle complet d'Impression → Placement → Redistribution. |
Défi clé | - | Contrôle du deuxième profil de refusion pour éviter que les composants situés sur la face supérieure (maintenant suspendus à l'envers) ne tombent, en particulier les plus lourds. |
Application typique | Des cartes plus simples comme des télécommandes, des alimentations. | Produits haute densité tels que les cartes mères de smartphones, les ordinateurs portables et les modules de communication. |
IV. Analyse des défauts SMT et renforcement de la qualité
Top 4 des solutions aux défauts
Type de défaut | Cause profonde typique | Mesures correctives/préventives |
---|---|---|
Tombstoneing | Masse thermique inégale sur les deux pads d'un composant, provoquant la fusion de la soudure à des moments différents. | Optimiser la conception des pastilles PCB pour la symétrie thermique (DFM) ; optimiser la zone de préchauffage par refusion. |
Billes de soudure | Humidité dans la pâte à souder ou flux trop agressif ; la vitesse de préchauffage est trop rapide. | Stockez et manipulez la pâte à souder conformément aux spécifications ; ralentissez la vitesse de préchauffage. |
Joint de soudure à froid | Température de pointe ou temps insuffisant dans la zone de refusion ; oxydation du tampon. | Optimiser le profil thermique de refusion ; assurer une bonne soudabilité des PCB et des composants. |
Vidange du BGA | Les matières volatiles du flux ne parviennent pas à s'échapper complètement avant que le joint de soudure ne se solidifie. | Utiliser une pâte à souder à faible émission de vides ; optimiser la conception de l'ouverture du pochoir (par exemple, les vitres) ; optimiser le profil thermique. |
Les deux piliers des systèmes de qualité
- DFM (Conception pour la fabricabilité)
- Prendre en compte les limites du processus de fabrication pendant la phase de conception du produit, telles que l'espacement des composants, la conception des pastilles et le placement des repères.
- Mise en œuvre de la norme IPC
- Adhérant aux normes d'assemblage électronique reconnues internationalement, telles que IPC-A-610 (Acceptabilité des assemblages électroniques) et J-STD-001 (Exigences relatives aux assemblages électriques et électroniques soudés).
V. Tendances émergentes en SMT
- Usine intelligente et Industrie 4.0:Connecter tous les équipements via un MES (Manufacturing Execution System) pour une surveillance des données en temps réel, une traçabilité et une prise de décision intelligente afin d'optimiser l'OEE (Overall Equipment Effectiveness).
- Intégration fine et hétérogène:Demandes croissantes d'assemblage de composants sub-01005 et de modules SiP (System-in-Package) haute densité.
- Fabrication verte:Utilisation de flux à faible teneur en COV ou sans nettoyage et d'équipements économes en énergie pour réduire l'impact environnemental.
Conclusion : Le chemin du raffinement ne s'arrête jamais
Lorsqu'une carte mère haute densité, composée de milliers de composants, est produite efficacement sur une ligne CMS, elle représente une fusion parfaite entre science des matériaux, ingénierie de précision, optique et logiciel. La maîtrise du processus CMS est essentielle pour accéder à la fabrication électronique moderne. Seule l'innovation technologique permet de progresser sur cette voie d'amélioration continue.
Annexe : Foire aux questions (FAQ)
Q1 : Comment choisir une machine pick-and-place ?
R : Les indicateurs clés incluent la vitesse théorique (CPH), le débit réel (UPH), la précision de placement (μm), la gamme de composants pris en charge et le temps de changement. Le choix dépend d'une évaluation complète du type de produit et du volume de production.
Q2 : Le procédé adhésif (colle rouge) est-il obsolète ?
R : Dans les assemblages mixtes (CMS + THT) nécessitant un brasage à la vague, le procédé adhésif reste indispensable pour fixer les composants CMS. Cependant, il est rarement utilisé dans les procédés de refusion double face.
Q3 : L'inspection SPI 100% est-elle nécessaire ?
R : Pour les produits à haute fiabilité (par exemple, automobiles, médicaux, aérospatiaux) et les circuits imprimés haute densité à pas fin, l'inspection SPI 100% est obligatoire. L'industrie automobile exige souvent un indice de capabilité des processus (Cpk) ≥ 1,67, ce qui indique un taux de défauts potentiels extrêmement faible, garanti uniquement par l'inspection 100%.
Q4 : Comment optimiser la consommation d'énergie du four de refusion ?
R : Les fours à refusion modernes peuvent être plus économes en énergie que les modèles plus anciens en utilisant des systèmes de récupération de chaleur à plusieurs étages, des matériaux d'isolation améliorés et des modes de veille intelligents.
Agissez maintenant :
Obtenez votre liste de contrôle DFM de ligne SMT
Abonnez-vous à notre hebdomadaire sur la fabrication électronique pour découvrir plus de secrets de processus !
(Remarque : les données de cet article sont tirées des normes IPC, des livres blancs techniques sur les équipements et des meilleures pratiques du secteur. Certains chiffres sont des exemples typiques ; les valeurs réelles dépendent du processus spécifique.)