Introdução: Uma revolução industrial no microcosmo
Desde processadores para smartphones e placas de controlo de dispositivos médicos a sensores electrónicos para automóveis, a criação deste hardware de precisão depende de Tecnologia de montagem em superfície (SMT). Em comparação com a tradicional tecnologia de orifícios (THT), a SMT fez avançar a indústria eletrónica com três inovações fundamentais:
- Miniaturização: As dimensões dos componentes diminuíram para 01005 (0,4×0,2 mm), permitindo densidades de montagem várias vezes superiores às da THT.
- Automatização de alto nível: As máquinas pick-and-place de topo de gama podem atingir velocidades de 250.000 CPH (componentes por hora) com uma precisão de colocação que atinge o nível de ±15μm.
- Elevada fiabilidade: As juntas de solda formadas por soldadura por refluxo oferecem uma resistência mecânica e um desempenho elétrico superiores, com uma consistência muito superior à da soldadura manual.
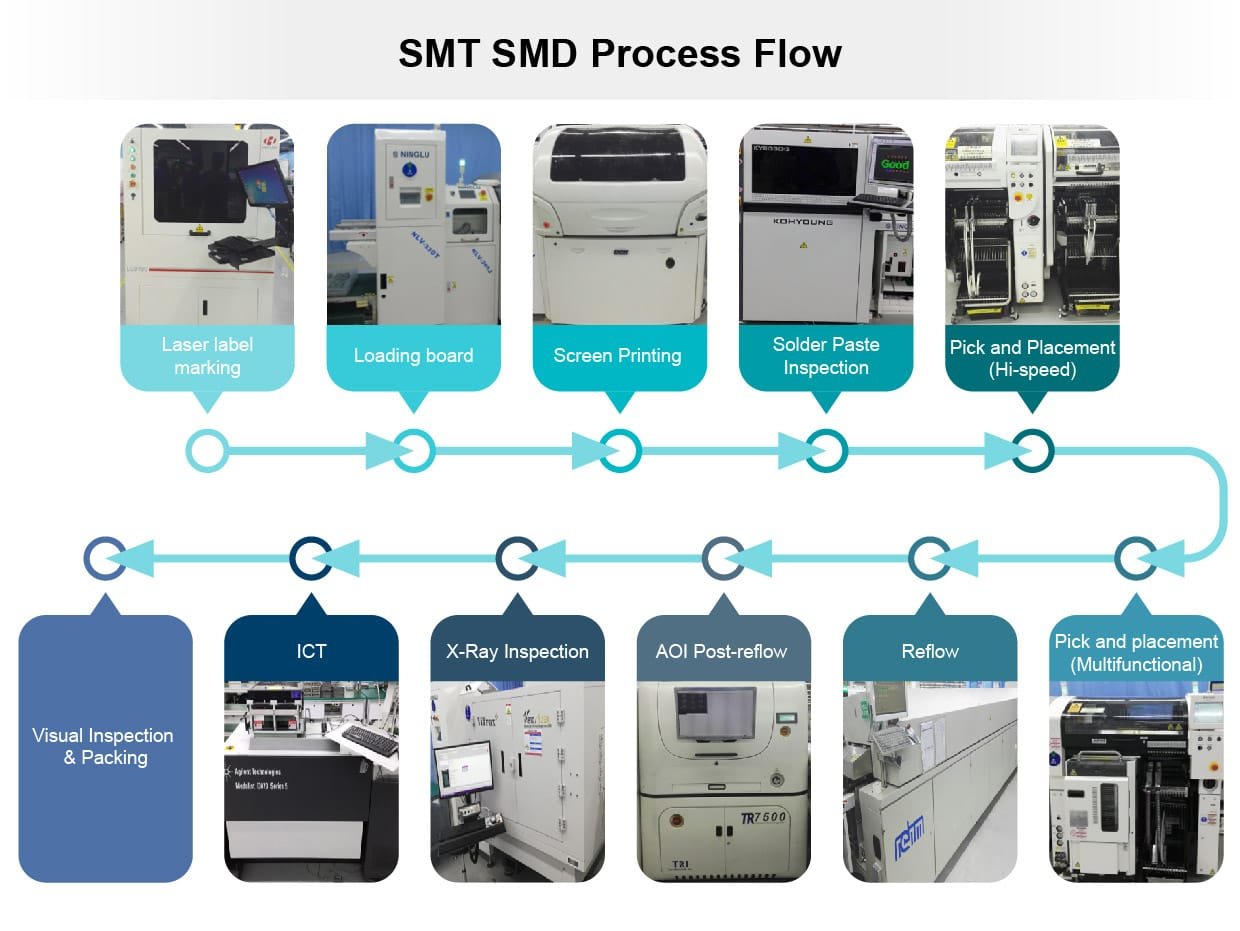
I. Visão geral do fluxograma do processo SMT
Um processo SMT completo funciona como uma linha de montagem de precisão em que cada fase é crítica.
gráfico LR
A[Carregamento de PCB
(Loader)] --> B[Impressão de pasta de solda
(Printer)]
B --> C[INSPECÇÃO 3D SPI
(Inspeção de pasta de solda)]
C --> D[Colocação de componentes
(Montador)]
D --> E[Soldadura por Refluxo
(Forno de Refluxo)]
E --> F[AOI
(Inspeção ótica automatizada)]
F --> G{Tem BGA/QFN
ou outras juntas ocultas?}
G -- Sim --> H[Inspeção por raios X]
H --> I[Descarga / Processo seguinte]
G -- Não --> I
II. Explicação das principais etapas do processo SMT
Passo 1: Carregamento e pré-processamento de PCB
- Equipamento essencial: Carregador automático de PCB
- Fundamentos do pré-processamento:
- Cozedura para desumidificação: Normalmente, a cozedura a 125°C durante várias horas remove a humidade do substrato e dos componentes da placa de circuito impresso, impedindo a "formação de bolhas" (delaminação) durante a soldadura a alta temperatura.
- Proteção ESD: O ambiente deve ter controlos rigorosos de temperatura e humidade (por exemplo, 45%-70% humidade) e todo o pessoal deve usar pulseiras ESD para proteger os componentes sensíveis.
Passo 2: Impressão de pasta de solda - Onde a precisão determina o sucesso
Este passo aplica com precisão uma quantidade definida de pasta de solda nas almofadas da placa de circuito impresso, preparando-as para a soldadura de componentes.
Elemento | Exemplo de especificações técnicas | Impacto |
---|---|---|
Estêncil | Cortado a laser, precisão da abertura ±5μm, electropolido | Garante uma elevada eficiência de transferência de pasta de solda (>90%) e uma definição de impressão limpa. |
Pasta de solda | Tamanho do pó tipo 4 (20-38μm), viscosidade 800-1000 kcps | Reduz os riscos de deslizamento e de formação de pontes após a impressão. |
Rodo | Poliuretano ou metal, dureza 80-90 Shore A, ângulo 45°-60° | Garante uma espessura de impressão uniforme e consistente. |
Passo 3: SPI - A primeira linha de defesa contra defeitos de soldadura
A SPI (Inspeção de pasta de solda) utiliza tecnologia ótica 3D para inspecionar o volume, a área, a altura e a forma da pasta de solda em cada almofada, o que a torna um ponto crítico de controlo do processo.
# Exemplo de lógica para uma verificação de aprovação/reprovação da inspeção da pasta de soldadura
def check_paste(paste_data):
# Nota: Os limiares são definidos por requisitos específicos do produto e do processo.
height_ok = 0.08 <= paste_data.height = 70
area_ok = paste_data.area_coverage >= 80
se altura_ok e volume_ok e área_ok:
return "PASS"
senão:
# Acciona um alarme e solicita a limpeza do estêncil ou o ajuste de parâmetros
devolver "FAIL - Acionar alarme"

As estatísticas do sector mostram que a SPI pode evitar mais de 70% de potenciais defeitos de soldadura causados por uma má impressão da pasta de solda.
Passo 4: Colocação de componentes - Um jogo de precisão ao nível do mícron
- Equipamento essencial: Máquina Pick-and-Place (ou montadora), disponível como disparador de chips de alta velocidade e montadora flexível de alta precisão.
- Tecnologias de base:
- Alinhamento da visão: Utiliza câmaras para reconhecer marcas fiduciais na placa de circuito impresso e nos condutores dos componentes para uma colocação de alta precisão (a precisão comum é de ±0,05 mm).
- Tecnologia de bicos: Muda automaticamente os bicos com base no tamanho e na forma dos componentes, recolhendo-os com um sistema de vácuo.
- Proteção contra erros: Verifica as informações sobre os componentes através da leitura de códigos de barras nos alimentadores para evitar peças erradas; utiliza câmaras ou sensores laser para verificar a orientação dos componentes, evitando o entupimento ou a inversão de polaridade.
Passo 5: Soldadura por refluxo - A arte do perfil térmico
A placa de circuito impresso, com os componentes nela colocados, passa por um forno em forma de túnel com várias zonas de aquecimento. A pasta de solda derrete e depois arrefece para formar ligações eléctricas e mecânicas fiáveis.
Um perfil térmico ideal (Exemplo para a solda SAC305 sem chumbo):
gráfico TD
A(Entrada) --> B[Zona de pré-aquecimento
Rampa para 150-180°C
60-90s]
B --> C[Zona de imersão / ativação
Manter a 180-220°C
60-120s]
C --> D[Zona de Refluxo
Temperatura de pico 240-250°C
45-60s acima do estado líquido]
D --> E[Zona de arrefecimento
Taxa de arrefecimento F(Saída)

Para placas de alta densidade ou sensíveis ao calor, Azoto (N₂) é frequentemente utilizado para criar uma atmosfera inerte. Manter os níveis de oxigénio extremamente baixos (por exemplo, <500 ppm) reduz a oxidação e melhora a qualidade da junta de soldadura.
Passo 6: AOI - O Inspetor de Visão Inteligente
A AOI (Inspeção Ótica Automatizada) é realizada após o refluxo para inspecionar automaticamente o PCBA quanto a defeitos de soldadura.
- Defeitos detectados: Componentes em falta, peças erradas, polaridade invertida, deslocação de componentes, tombstoning, bridging, bolas de solda e solda insuficiente.
- Evolução tecnológica: Os sistemas AOI modernos utilizam cada vez mais algoritmos de IA baseados na aprendizagem profunda. Treinados em vastas bibliotecas de imagens de defeitos, melhoram significativamente a precisão da deteção e reduzem as chamadas falsas.
Passo 7: Inspeção por raios X (para juntas de soldadura ocultas)
Para componentes como BGAs, QFNs e LGAs com juntas de solda sob a embalagem, a AOI é ineficaz. A inspeção por raios X pode penetrar no chip para visualizar claramente as ligações internas da esfera de solda.
- Principais pontos de inspeção: Curtos-circuitos de solda, circuitos abertos (não molhados) e o tamanho e a percentagem de vazios (por exemplo, as normas IPC podem exigir que os vazios sejam <25%).
III. SMT de uma face vs. SMT de duas faces: uma comparação de processos
Dependendo da conceção do produto, os PCBAs podem ser de uma ou duas faces, sendo que a última envolve um processo mais complexo.
Diferença de processo | Montagem de uma face | Montagem em duas faces (primeiro em cima, depois em baixo) |
---|---|---|
Primeiro lado (topo) Processo | Fluxo SMT completo (Imprimir → Colocar → Refluxo) | Fluxo SMT completo (Imprimir → Colocar → Refluxo) |
Inversão de quadros | N/A | Utiliza um módulo inversor dedicado na linha para uma transição suave. |
Segundo lado (inferior) Processo | N/A | Outro ciclo completo de Impressão → Colocação → Refluxo. |
Desafio-chave | - | Controlo do segundo perfil de refusão para evitar que os componentes do lado superior (agora pendurados ao contrário) caiam, especialmente os mais pesados. |
Aplicação típica | Placas mais simples, como controlos remotos e fontes de alimentação. | Produtos de alta densidade, como placas-mãe de smartphones, computadores portáteis e módulos de comunicação. |
IV. Análise de defeitos de SMT e reforço da qualidade
As 4 principais soluções para defeitos
Tipo de defeito | Causa raiz típica | Ação corretiva/preventiva |
---|---|---|
Tombamento | Massa térmica desigual nas duas almofadas de um componente, fazendo com que a solda derreta em momentos diferentes. | Otimizar a conceção do bloco de PCB para simetria térmica (DFM); otimizar a zona de pré-aquecimento do refluxo. |
Bolas de solda | Humidade na pasta de solda ou fluxo demasiado agressivo; a taxa de rampa de pré-aquecimento é demasiado rápida. | Armazenar e manusear a pasta de solda de acordo com as especificações; abrandar a velocidade da rampa de pré-aquecimento. |
Junta de solda a frio | Temperatura ou tempo de pico insuficientes na zona de refluxo; oxidação da almofada. | Otimizar o perfil térmico de refluxo; assegurar uma boa soldabilidade de PCBs e componentes. |
Vazamento de BGA | Os voláteis do fluxo não conseguem escapar completamente antes da solidificação da junta de solda. | Utilizar pasta de solda com baixo teor de vazamento; otimizar a conceção da abertura do estêncil (por exemplo, painéis de janela); otimizar o perfil térmico. |
Os dois pilares dos sistemas de qualidade
- DFM (Design for Manufacturability)
- Considerar as limitações do processo de fabrico durante a fase de conceção do produto, tais como o espaçamento dos componentes, a conceção das almofadas e a colocação de fiduciais.
- Implementação da norma IPC
- Cumprimento de normas de montagem de eletrónica reconhecidas internacionalmente, tais como IPC-A-610 (Aceitabilidade dos conjuntos electrónicos) e J-STD-001 (Requisitos para conjuntos eléctricos e electrónicos soldados).
V. Tendências emergentes no domínio da SMT
- Fábrica inteligente e indústria 4.0: Ligação de todo o equipamento através de um MES (Manufacturing Execution System) para monitorização de dados em tempo real, rastreabilidade e tomada de decisões inteligentes para otimizar o OEE (Overall Equipment Effectiveness).
- Integração fina e heterogénea: Procura crescente de montagem de componentes sub-01005 e de módulos SiP (System-in-Package) de alta densidade.
- Fabrico ecológico: Utilização de fluxos com baixo teor de COV ou sem limpeza e equipamento energeticamente eficiente para reduzir o impacto ambiental.
Conclusão: O caminho do aperfeiçoamento nunca termina
Quando uma placa-mãe de alta densidade com milhares de componentes flui eficientemente numa linha SMT, representa uma fusão perfeita de ciência dos materiais, engenharia de precisão, ótica e software. Dominar o processo SMT principal é a chave para entrar no mundo do fabrico moderno de produtos electrónicos. Só abraçando continuamente a inovação tecnológica é que se pode prosperar neste caminho de melhoria constante.
Apêndice: Perguntas mais frequentes (FAQ)
Q1: Como escolher uma máquina pick-and-place?
R: As principais métricas incluem a velocidade teórica (CPH), o rendimento real (UPH), a precisão de colocação (μm), a gama de componentes suportados e o tempo de mudança. A escolha depende de uma avaliação exaustiva do tipo de produto e do volume de produção.
Q2: O processo de adesivo (cola vermelha) é obsoleto?
R: Em montagens de tecnologia mista (SMT + THT) que requerem soldadura por onda, o processo adesivo continua a ser indispensável para fixar os componentes SMT. No entanto, raramente é utilizado em processos de refluxo puramente de dupla face.
Q3: É necessária a inspeção SPI do 100%?
R: Para produtos de alta fiabilidade (por exemplo, automóveis, médicos, aeroespaciais) e PCBAs de alta densidade e passo fino, o 100% SPI é obrigatório. A indústria automóvel exige frequentemente um índice de capacidade de processo (Cpk) de ≥ 1,67, o que significa uma taxa de defeitos potenciais extremamente baixa que só pode ser assegurada através da inspeção 100%.
Q4: Como pode ser optimizado o consumo de energia do forno de refluxo?
R: Os fornos de refluxo modernos podem ser mais eficientes em termos energéticos do que os modelos mais antigos, utilizando sistemas de recuperação de calor de várias fases, materiais de isolamento melhorados e modos de espera inteligentes.
Atuar agora:
Obtenha sua lista de verificação de DFM da linha SMT
Subscreva a nossa revista Electronics Manufacturing Weekly para desvendar mais segredos de processos!
(Nota: Os dados neste artigo são citados a partir de padrões IPC, white papers técnicos de equipamentos e melhores práticas da indústria. Algumas figuras são exemplos típicos; os valores reais dependem do processo específico).