はじめに:ミクロの世界における製造業の革命
スマートフォンのプロセッサや医療機器の制御基板から自動車の電子センサーまで、こうした精密ハードウェアの製造には 表面実装技術(SMT)従来のスルーホール技術(THT)と比較して、SMTは次の3つの重要な革新によってエレクトロニクス業界を前進させました。
- 小型化部品サイズは01005(0.4×0.2mm)まで縮小され、THTよりも数倍高い組み立て密度を実現しています。
- 高度な自動化: トップクラスのピックアンドプレース マシンは、250,000 CPH (1 時間あたりのコンポーネント数) の速度と ±15μm レベルの配置精度を実現します。
- 高い信頼性リフローはんだ付けによって形成されたはんだ接合部は、手作業によるはんだ付けをはるかに上回る一貫性を備え、優れた機械的強度と電気的性能を備えています。
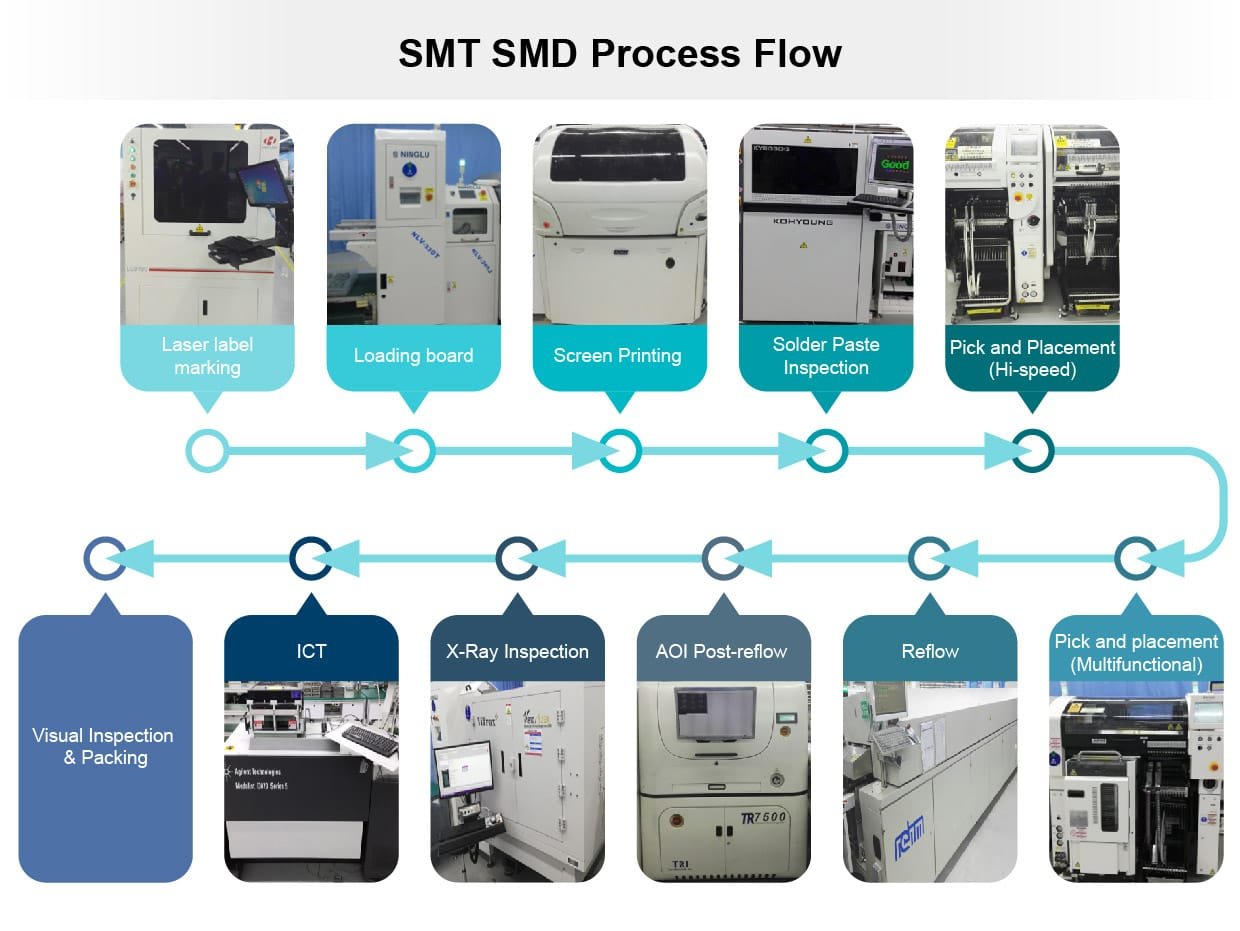
I. SMTプロセスフローチャートの概要
完全な SMT プロセスは、すべての段階が重要である精密な組立ラインのように動作します。
グラフLR A[PCBローディング(ローダー)] --> B[はんだペースト印刷(プリンター)] B --> C[3D SPI(はんだペースト検査)] C --> D[部品配置(マウント)] D --> E[リフローはんだ付け(リフローオーブン)] E --> F[AOI(自動光学検査)] F --> G{BGA/QFNまたはその他の隠れた接合部がありますか?} G -- はい --> H[X線検査] H --> I[アンローディング/次のプロセス] G -- いいえ --> I
II. コアSMTプロセスステップの説明
ステップ1:PCBのロードと前処理
- 主要装備: 自動PCBローダー
- 前処理の基本:
- 除湿のためのベーキング: 通常、125°C で数時間焼成して PCB 基板とコンポーネントから水分を除去し、高温はんだ付け中の「ポップコーン」(層間剥離) を防止します。
- ESD保護: 環境には厳格な温度と湿度の制御(例:湿度 45%-70%)が必要であり、敏感なコンポーネントを保護するためにすべての担当者が ESD リスト ストラップを着用する必要があります。
ステップ2:はんだペースト印刷 – 精度が成功を左右する
このステップでは、定義された量のはんだペーストを PCB のパッドの上に正確に塗布し、コンポーネントのはんだ付けの準備をします。
要素 | 技術仕様の例 | インパクト |
---|---|---|
ステンシル | レーザーカット、開口精度±5μm、電解研磨 | 高いはんだペースト転写効率 (>90%) ときれいな印刷定義を保証します。 |
はんだペースト | タイプ4の粉末サイズ(20〜38μm)、粘度800〜1000 kcps | 印刷後の垂れやブリッジのリスクを軽減します。 |
スクイジー | ポリウレタンまたは金属、硬度80~90ショアA、角度45°~60° | 均一で一貫した印刷厚さを保証します。 |
ステップ3:SPI – はんだ付け不良に対する第一防衛線
SPI (はんだペースト検査) は、3D 光学技術を使用して、すべてのパッド上のはんだペーストの量、面積、高さ、形状を検査するため、重要なプロセス制御ポイントとなります。
# はんだペースト検査の合否チェックのロジック例 def check_paste(paste_data): # 注: しきい値は、特定の製品およびプロセス要件によって定義されます。 height_ok = 0.08 <= paste_data.height <= 0.15 # (mm) volume_ok = paste_data.volume_percent >= 70 area_ok = paste_data.area_coverage >= 80 height_okかつvolume_okかつarea_okの場合: "PASS"を返し、そうでない場合: # アラームをトリガーし、ステンシルのクリーニングまたはパラメータ調整を促します。 "FAIL - アラームをトリガー"を返します。

業界統計によると、SPI は、はんだペーストの印刷不良によって引き起こされる潜在的なはんだ付け欠陥を 70% 以上防止できます。
ステップ4:部品の配置 – ミクロンレベルの精度
- 主要装備: ピックアンドプレースマシン(またはマウンター)、高速チップシューターと高精度フレキシブルマウンターとして利用可能。
- コアテクノロジー:
- ビジョンの調整: カメラを使用して PCB 上の基準マークとコンポーネントのリードを認識し、高精度な配置を実現します (一般的な精度は ±0.05 mm)。
- ノズル技術: 部品のサイズと形状に基づいてノズルを自動的に変更し、真空システムで部品を吸着します。
- エラー防止: フィーダー上のバーコードをスキャンしてコンポーネント情報を確認し、間違った部品を防止します。また、オンザフライ カメラまたはレーザー センサーを使用してコンポーネントの向きを確認し、トゥームストーンや極性反転を防止します。
ステップ5:リフローはんだ付け - 熱プロファイルの芸術
部品が配置されたPCBは、複数の加熱ゾーンを備えたトンネル状のオーブンを通過します。はんだペーストは溶融し、その後冷却されて、信頼性の高い電気的・機械的接続が形成されます。
理想的な熱プロファイル(鉛フリーSAC305はんだの例)
グラフTD A(入口) --> B[予熱ゾーンを150~180°Cに60~90秒加熱] B --> C[ソーク/活性化ゾーンを180~220°Cで60~120秒保持] C --> D[リフローゾーンのピーク温度240~250°C、液相線より45~60秒高い] D --> E[冷却ゾーンの冷却速度<4°C/秒] E --> F(出口)

高密度または熱に弱い基板の場合、 窒素(N₂) 不活性雰囲気を作り出すためによく使用されます。酸素濃度を極めて低く(例:500ppm未満)保つことで酸化が抑制され、はんだ接合部の品質が向上します。
ステップ6:AOI – インテリジェントビジョンインスペクター
リフロー後に AOI (自動光学検査) を実行し、PCBA のはんだ付け欠陥を自動的に検査します。
- 検出された欠陥: コンポーネントの不足、部品の間違い、極性の反転、コンポーネントのずれ、ツームストーン、ブリッジ、はんだボール、はんだ不足。
- 技術の進化現代のAOIシステムでは、ディープラーニングに基づくAIアルゴリズムの活用がますます増えています。膨大な欠陥画像ライブラリで学習させることで、検出精度が大幅に向上し、誤判定も減少します。
ステップ7:X線検査(隠れたはんだ接合部)
パッケージ下部にはんだ接合部を持つBGA、QFN、LGAなどの部品の場合、AOIは効果的ではありません。X線検査はチップを透過し、内部のはんだボール接合部を明確に視覚化できます。
- 主な検査ポイント: はんだのショート、開回路 (非ウェット)、およびボイドのサイズと割合 (例: IPC 規格では、ボイドが <25% であることが要求される場合があります)。
III. 片面SMTと両面SMT:プロセスの比較
製品設計に応じて、PCBA は片面または両面にすることができ、後者の場合はより複雑なプロセスが必要になります。
プロセスの違い | 片面アセンブリ | 両面組み立て(最初に上、次に下) |
---|---|---|
第一面(上面)プロセス | フルSMTフロー(印刷→配置→リフロー) | フルSMTフロー(印刷→配置→リフロー) |
ボードフリッピング | 該当なし | スムーズな移行のために、ラインに専用のインバータモジュールを使用します。 |
裏面(下面)の工程 | 該当なし | 印刷 → 配置 → リフローのもう 1 つの完全なサイクル。 |
主な課題 | — | 2 番目のリフロー プロファイルを制御して、上側のコンポーネント (逆さまにぶら下がっている) が落下するのを防ぎます (特に重いコンポーネント)。 |
典型的なアプリケーション | リモコンや電源などのよりシンプルなボード。 | スマートフォンのマザーボード、ラップトップ、通信モジュールなどの高密度製品。 |
IV. SMT欠陥分析と品質強化
欠陥解決策トップ4
欠陥の種類 | 典型的な根本原因 | 是正措置/予防措置 |
---|---|---|
墓石 | コンポーネントの 2 つのパッドの熱質量が不均一であるため、はんだが異なるタイミングで溶けます。 | 熱対称性 (DFM) のために PCB パッド設計を最適化し、リフロー予熱ゾーンを最適化します。 |
はんだボール | はんだペースト内の水分または過度に強力なフラックス、予熱のランプ速度が速すぎます。 | はんだペーストは仕様に従って保管および取り扱い、予熱のランプ速度を遅くしてください。 |
冷間はんだ接合 | リフローゾーンのピーク温度または時間が不十分、パッドが酸化される。 | リフロー熱プロファイルを最適化し、PCB とコンポーネントの良好なはんだ付け性を確保します。 |
BGAボイド | フラックスの揮発性物質は、はんだ接合部が固まる前に完全に逃げることができません。 | 低空隙はんだペーストを使用し、ステンシル開口部の設計を最適化します (例: ウィンドウ ペイン)。熱プロファイルを最適化します。 |
品質システムの二つの柱
- DFM(製造性を考慮した設計)
- 製品設計段階で、コンポーネントの間隔、パッド設計、基準点の配置など、製造プロセスの制限を考慮します。
- IPC標準の実装
- 国際的に認められた電子機器組立基準に準拠し、 IPC-A-610 (電子アセンブリの許容性)および J-STD-001 (はんだ付けされた電気および電子アセンブリの要件)。
V. SMTの新たなトレンド
- スマートファクトリーとインダストリー4.0: すべての機器を MES (製造実行システム) を介して接続し、リアルタイムのデータ監視、トレーサビリティ、インテリジェントな意思決定を行って OEE (総合設備効率) を最適化します。
- ファインピッチと異種統合: サブ01005コンポーネントおよび高密度SiP(システムインパッケージ)モジュールの組み立てに対する需要の増加。
- グリーン製造: 環境への影響を軽減するために、低 VOC または無洗浄フラックスとエネルギー効率の高い機器を使用します。
結論:洗練の道は決して終わらない
数千個の部品を搭載した高密度マザーボードがSMTラインを効率的に流れていくとき、それは材料科学、精密工学、光学、そしてソフトウェアの完璧な融合を意味します。SMTの中核プロセスを習得することが、現代の電子機器製造の世界に参入するための鍵となります。技術革新を継続的に受け入れることによってのみ、この絶え間ない改善の道を歩み続けることができるのです。
付録: よくある質問 (FAQ)
Q1: ピックアンドプレースマシンはどのように選択しますか?
A: 主要な指標としては、理論速度(CPH)、実世界スループット(UPH)、実装精度(μm)、対応部品範囲、段取り替え時間などが挙げられます。選定は、製品の種類と生産量を総合的に評価した上で決定されます。
Q2: 接着剤(赤糊)の工程は時代遅れですか?
A: ウェーブはんだ付けを必要とする複合技術実装(SMT + THT)では、SMT部品の固定に接着工程が依然として不可欠です。ただし、純粋な両面リフロー工程ではほとんど使用されません。
Q3: 100% SPI検査は必要ですか?
A: 高信頼性製品(例:自動車、医療、航空宇宙)および高密度・ファインピッチPCBAの場合、100% SPIは必須です。自動車業界では、工程能力指数(Cpk)が1.67以上であることが求められることが多く、これは潜在的欠陥率が極めて低いことを意味し、100%検査によってのみ保証されます。
Q4: リフロー炉のエネルギー消費を最適化するにはどうすればよいですか?
A: 最新のリフロー炉は、多段熱回収システム、改良された断熱材、インテリジェントなスタンバイ モードを使用することで、旧モデルよりも 30% 以上エネルギー効率が向上します。
今すぐ行動を起こしましょう:
SMTラインDFMチェックリストを入手する
さらなるプロセスの秘密を知るには、Electronics Manufacturing Weekly を購読してください。
(注:この記事のデータは、IPC 標準、機器の技術ホワイト ペーパー、業界のベスト プラクティスから引用されています。一部の数値は一般的な例であり、実際の値は特定のプロセスによって異なります。)